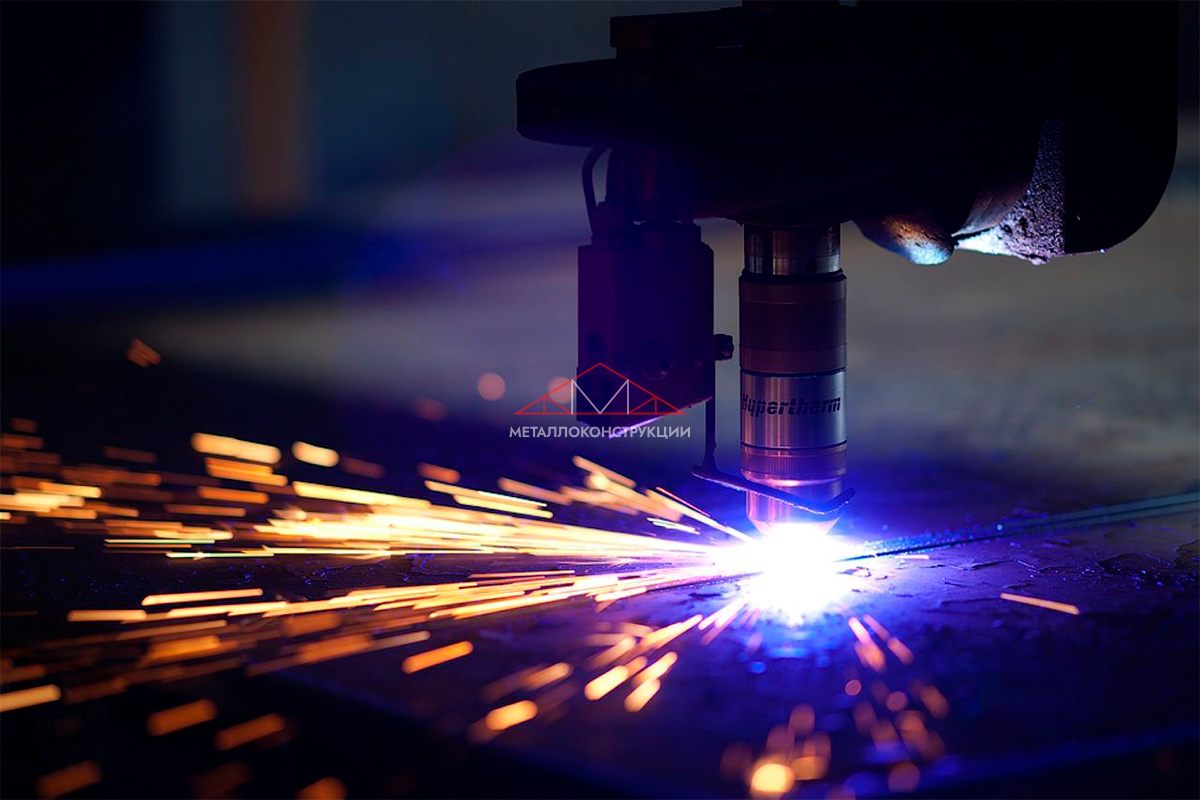
Плазменная резка – вид термической обработки материала, отличающийся своей технологичностью и универсальностью. Применяют для раскроя практически всех металлов, а для обработки высоколегированной стали такая технология не имеет аналогов. Плазменные станки оснащены числовым программным управлением (ЧПУ), благодаря чему открывается возможность для фигурной резки и создания сложных узоров: достаточно ввести нужную программу и процесс запустится автоматически.
В сегодняшней статье подробнее рассмотрим особенности плазменных станков и разберем, какие характеристики важно учитывать при выборе оборудования.
Устройство станка для плазменной резки и принципы его работы
Плазменная резка осуществляется за счет быстрого нагрева металла до высоких температур. Материал расплавляется и удаляется обдувом в зоне раскроя. В качестве резца используют струи плазмы – ионизированный газ, разогретый до 5000 – 30000 ℃. Он на огромной скорости вырывается из сопла плазмотрона и контактирует с обрабатываемой поверхностью. Станок состоит из следующих основных элементов:
- Рабочая поверхность. Представляет собой стол с системой крепежа заготовки. Рабочее поле сильно отличается по габаритам и зависит от требований и возможностей конкретного производства;
- Направляющие приводы. Обеспечивают точное перемещение инструмента относительно заготовки, двигая резаком вдоль осей ;
- Панель управления (система ЧПУ). В нее входит компьютер, управляющий резаком. Оператор станка задает требуемые параметры, благодаря чему осуществляется высокоточная автоматизированная резка;
- Резак. Основной рабочий элемент, состоит из сопла, в котором формируются плазменные струи, электрода, генерирующего дугу и системы охлаждения;
- Источник питания и газа. Отвечает за контроль давления и расход газа, необходимого для формирования плазмы.
При работе со станком между электродом и соплом генерируется дуга, которая контактирует с поверхностью заготовки. С этого начинается плазменная резка. Рабочий газ делится внутри плазмотрона на плазмообразующий и защитный поток. Первый отвечает за раскрой, а второй за охлаждение головки резака.
Виды плазмотронов
Существуют различные способы классификации плазмотронов. По способу генерации плазмы выделяют:
- Электродуговые – оборудованные как минимум одним катодом и анодом. В качестве охлаждающей жидкости выступает вода.
- Высокочастотные – используют индуктивную или емкостную связь с источником питания. В конструкции не предусмотрен катод – разрядные камеры изготавливают из кварцевого стекла или керамики. Для работы не требуется электрического контакта между электродами и плазмой, что позволяет избежать перегрева. Для охлаждения используется простая воздушная система.
- Комбинированные – сочетают использования токов высокой частоты и поддержание сжимаемого магнитным полем дугового разряда.
Существуют другие подходы к классификации плазменных резаков. Например, по способу получения дуги выделяют устройства с высокочастотным и пневматическим поджигом. В первом случае используется осциллятор (устройство для бесконтактного возбуждения сварочной дуги), во втором – происходит замыкание в единую цепь электрода, сопа и свариваемой поверхности.
Процесс плазменной резки
- Создание программы резки, описывающей траекторию движения плазменной головки, скорость разреза и иные параметры.
- Подача напряжения с помощью трансформатора или инвертора. Выбор источника питания зависит от нужд конкретного производства. Трансформатор предназначен для длительной работы и разрезает металл большей толщины, а инвертор обладает меньшим весом и стоимостью, но справляется только с тонкими заготовками.
- Поступление тока в плазморез, разжигание первичной дуги.
- Подача воздуха через компрессор. Под действием потока плазмы разогревается до заданной температуры, образуя дугу для раскроя.
- Проверка изделия на неровность кромки по завершении обработки.
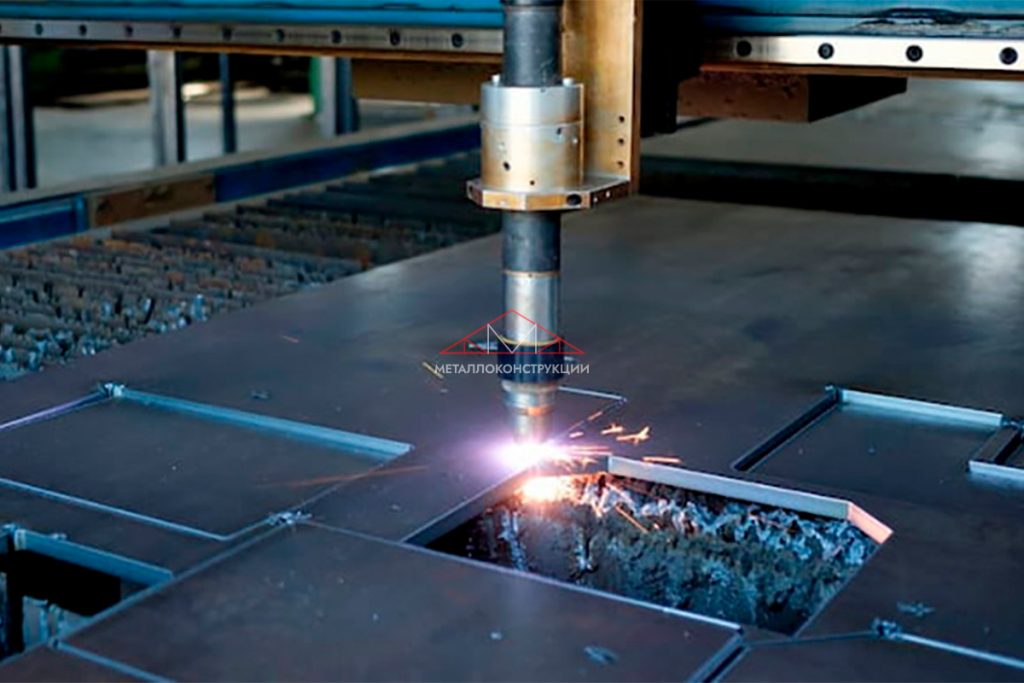
Стационарные, мобильные и промышленные плазморезы
Станки для плазменной раскройки делят на три группы, в зависимости от их габаритов и производственных мощностей:
- Устройства для ручной резки. Это небольшой блок питания с плазмотроном, газовой смесью и компрессором. Негабаритная аппаратура, недорогая, доступная для использования в любом помещении. Главный недостаток – малая мощность и невозможность добиться высокой точности, особенно при работе с толстыми металлами.
- Портативные установки. Среднее по весу и габаритам оборудование, оснащенное блоком ЧПУ. Управление осуществляется через встроенную клавиатуру и жидкокристаллический экран. Мобильные установки сочетают точность, скорость и качество раскроя, при этом все процессы автоматизированы, что позволяет добиться повторяемости узора. Но для промышленного массового производства такие станки не подойдут ввиду недостаточной мощности.
- Стационарные промышленные станки. Применяются на конвейерных линиях, отличаются исключительной точностью реза и запрограммированностью действий. Для работы с такой аппаратурой требуется специально обученный оператор. Стационарные плазменные станки дают максимально возможную точность раскроя, справляются с толстыми металлами, выполняют сложные орнаменты. Но стоить оборудование дорого и не всегда покупка будет оправдана.
Как выбрать станок для плазменной резки
Как мы видим, на рынке представлено огромное количество плазморезов, отличающихся по комплектации, мощности, габаритам и целям. При выборе устройства обращайте внимание на диапазон толщины обрабатываемого материала, решаемые задачи и условия эксплуатации. Основные характеристики, которые стоит учитывать:
- Производственные мощности. Примерно рассчитывайте, исходя из соотношения 4 ампера на 1 мм углеродистой стали и 6 ампер на 1 мм алюминия или нержавейки.
- Время беспрерывной работы. От данного параметра зависит, сможете ли вы получить требуемую деталь без прерывания цикла.
- Параметры сети и потребляемая мощность. Ваша сеть должна выдержать предполагаемую нагрузку и обеспечить стабильную и непрерывную работу станка.
Также обязательно изучите такие характеристики как размер рабочего стола, скорость перемещения головки, точность позиционирования.
На нашем производстве мы используем современные и мощные плазменные станки с рабочими столами до 12 метров, так что мы сможем реализовать даже самые амбициозные ваши цели.
Оставьте заявку прямо сейчас и получите подробное коммерческое предложение с расчётами и сроками производства металлоконструкций под ключ.
Оставить заявку