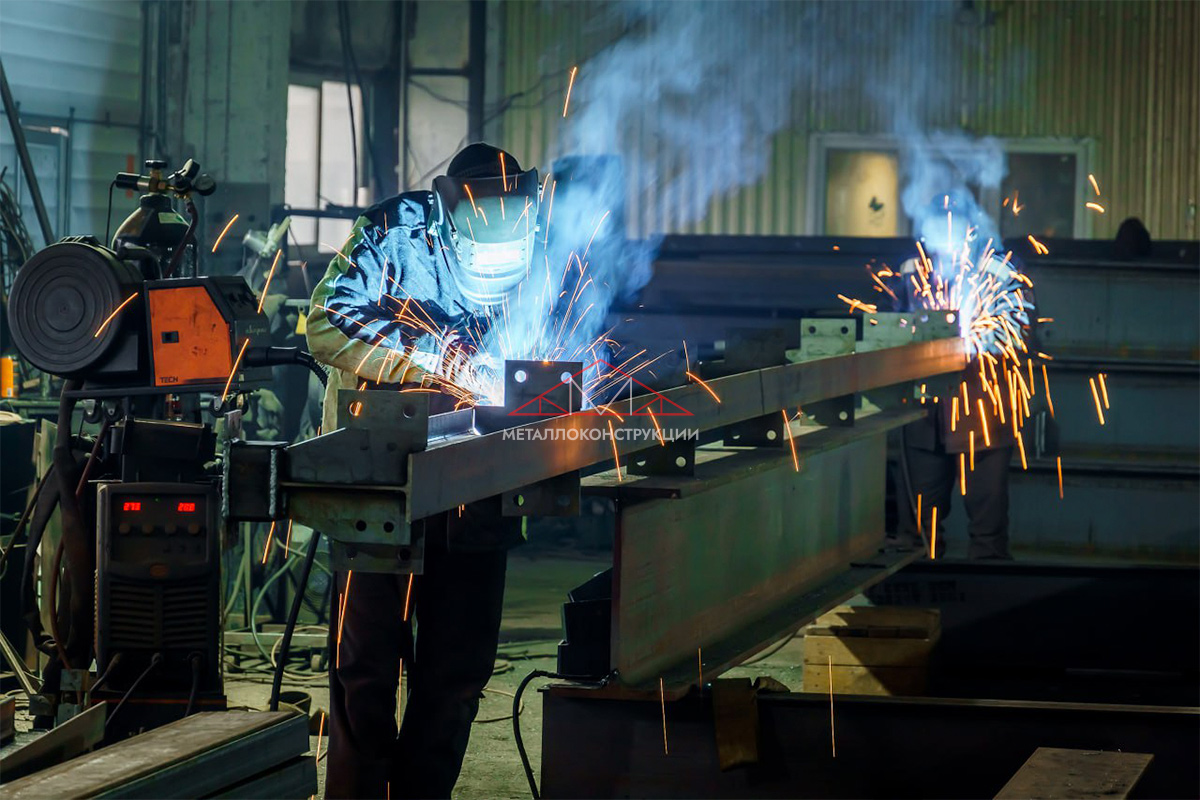
Изготовление металлических изделий (МИ) представляет собой многоступенчатый процесс создания конструкций строительного и сельскохозяйственного назначения, деталей машин и механизмов, изделий для бытовых нужд и других металлических заготовок.
Классификация изделий
МИ классифицируют по разным критериям. Наиболее популярна классификация по форме сечения:
- Сортовой — заготовки, полученные путем прокатки на станах. Имеют форму кругов, полос, квадратов и шестигранников;
- Трубный — заготовки в форме труб различного диаметра;
- Листовой — в форме плоских листов различных размеров и толщины;
- Фасонный — металлические изделия массового и специального назначения, выпускаемые в форме уголков, швеллеров, тавров.
По сути, изготовление металлических изделий — процесс производства компонентов, моделей или структурных элементов из металла с применением различных технологий Выбор метода создания или обработки определяется исходными свойствами материала и желаемыми характеристиками готового изделия. Производство МИ осуществляется с использованием следующих технологий:
- лазерная резка — воздействие высокочастотного луча лазера, который доводит металл до плавления, закипания, а затем вызывает полное сгорание или испарение;
- автоматизированная гибка с использованием станков и прессов с ЧПУ;
- механизированная рубка — первичная обработка с использованием гильотины, станков с программным управлением, режущих прессов;
- сварка — соединение металлов путем их нагрева и последующего охлаждения;
- токарная металлообработка — резание, торцевание, снятие фасок, прорезание канавок, нарезание внутренних и наружных резьб.
Технология производства
Выпуску МИ предшествует разработка проекта. Составляются чертежи с указанием точных размеров и пропорций деталей. В разработку попадают как схематическое изображение, так и 3D модель.
В зависимости от особенностей технологии, количество этапов варьируется. В этой статье подробно рассмотрим 7 стадий:
- Выбор материалов.
- Формовка.
- Механическая обработка.
- Термическая обработка.
- Вторичная обработка.
- Соединение.
- Финишная обработка.
1 этап. Выбор материалов
Предприятия, располагающие собственным сырьем и заготовками, логично пропускают этот этап. Компании без собственной сырьевой базы подбирают наиболее соответствующий техническому заданию материал, сотрудничая с сертифицированными поставщиками.
При подборе учитываются:
- физические, химические и механические свойства материала;
- назначение будущей детали;
- доступные технологии производства (литье, ковка, гибка, штамповка).
2 этап. Формообразование
Будущим деталям придается определенная форма и размер путем литья, резки, ковки, штамповки, прессования или другой технологии. Нужный метод выбирают в зависимости от пластичности, твердости и жаропрочности металла.
3 этап. Механическая обработка
Поверхность деталей обрабатывается вручную или автоматически с использованием металлорежущих станков. В зависимости от требований, предъявляемых к готовому изделию, обработка может включать:
- точение (удаление стружки с поверхности);
- фрезерование;
- сверление;
- шлифовку.
4 этап. Термическая обработка
Ряду МИ требуется устойчивость к перепадам температур, ударным и статическим нагрузкам. Устойчивость деталь приобретает при помощи термообработки — закалки или отжига.
5 этап. Вторичная обработка
В процессе вторичной обработки удаляют припуск (верхний слой металла), в результате чего остается минимальный дефектный слой. При необходимости изделия полируются с помощью полировальных кругов с мелкими абразивными зернами.
6 этап. Соединение деталей
В зависимости от особенностей изделия, для соединения используют специальные клеевые составы, сварку, клепки для несъмного соединения, болты, шпильки.
7 этап. Финишная обработка
Готовым деталям придается нужный оттенок или защитный слой путем порошкового окрашивания, хромирования, борирования, цинкования или гальванизации. После финишной обработки деталь подвергается контролю качества. Проверка МИ и поиск скрытых дефектов осуществляется с использованием следующих методов:
- Визуальный контроль — наиболее доступный и быстрый метод контроля, в процессе которого проверяют качество сборки, состояние сварных швов, наличие вмятин, ржавчины, наплывов. Метод является базовым и проводится с использованием простейших измерительных средств.
- Ультразвук (УЗК) — позволяет выявить скрытые от глаз дефекты, трещины и пустоты. Несмотря на высокую чувствительность и низкую стоимость, УЗК не дает представления о реальном размере и характере дефекта.
- Магнитный метод — предполагает использование магнитного порошка для выявления неметаллических включений, трещин и дефектов, расположенных на небольшой глубине.
- Акустический контроль — обладает высокой чувствительностью и используется для выявления дефектов независимо от их расположения.
- Капиллярный метод — основан на проникновении контрастного вещества в исследуемый объект. Позволяет выявить микродефекты, терморазрывы, шлифовочные деформации.
Дефекты возникают на разных стадиях технологического процесса:
- при нарушении температурного режима в процессе закалки и обжига — внутреннее напряжение металла и, как следствие, разрушение в процессе эксплуатации;
- неправильные размеры и конфигурация вследствие использования изношенных форм;
- несоответствие требованиям ГОСТ, вызванное длительной обработкой или использованием низкокачественных инструментов.
Оставьте заявку прямо сейчас и получите подробное коммерческое предложение с расчётами и сроками производства металлоконструкций под ключ.
Оставить заявку