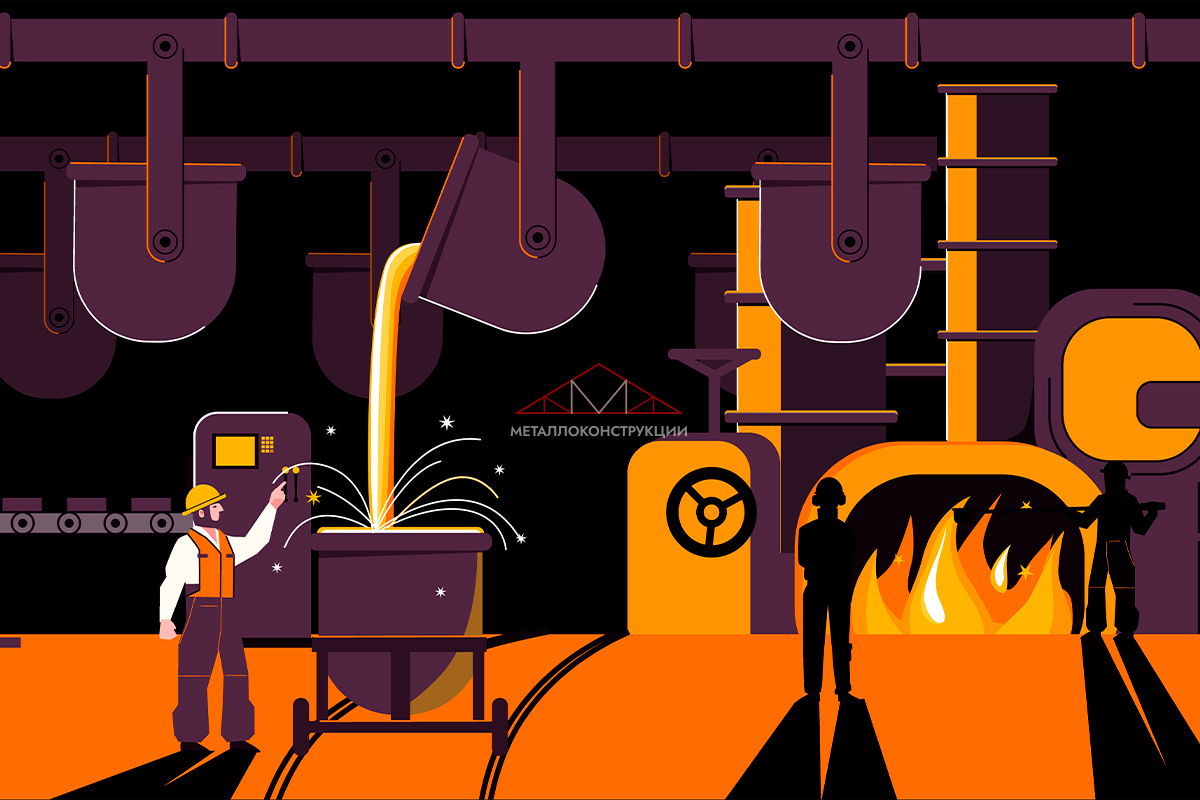
Металлообработка — совокупность процессов по оказанию физического воздействия на металлы и сплавы с помощью специальных инструментов. Таким образом изделию придают требуемую форму, размер и физико-химические свойства. История металлургии насчитывает более 5000 лет, с того момента как человек впервые добавил к расплавленной меди олово и получил бронзу. С тех пор появилось множество новых методов обработки материалов, решающих широкий спектр задач.
Сегодня ремесло кузнецов превратилось в сферу высоких технологий. Без металлообработки невозможно представить производство автомобилей и самолетов, строительство зданий и создание сложных гаджетов. Выделяют следующие типы обработки металла:
- Литье,
- Механообработка,
- Термическая,
- Электрическая,
- Сварка.
Разберем, какие инновации обнаруживаются в каждой области, а какие традиционные способы не утрачивают своей актуальности.
Литейное производство
Под литьем понимают процесс изготовления деталей путем заливки литейных форм расплавленным металлом. Наравне с холодной ковкой является одним из древнейших методов металлообработки. Современные технологии литья позволяют получить сложные детали, требующие минимальной механической постобработки.
Основные типы:
- Под давлением в пресс-формах. Расплавленный материал закачивается под давлением в трафарет, обеспечивая высокую точность и сложность детали. Применяется для отливки цветных металлов, таких как алюминий и цинк.
- В песчаных формах. Наиболее распространенный и бюджетный способ, эффективный при производстве грубых заготовок. Отверстия и полости в них образуют с помощью стержней, помещаемых в форму для литья.
- По выплавляемым моделям. Из стерина изготавливают высокоточную модель, а затем на нее наносят суспензию, формирующую оболочку. Таким образом гарантируется высокая детализация изделия.
- Центробежное литье. Материал заливается во вращающийся макет, где он равномерно распределяется под действием центробежной силы. Данный способ применим при изготовлении труб и других круглых деталей.
Преимущества:
- Универсальность — продукция любой сложности;
- Детализация — возможность добиться высокой степени проработанности;
- Скорость — подходит для выпуска массовой продукции.
Механическая обработка металла
В основе металлообработки на режущих станках лежит воздействие острой и твердой заготовкой на обрабатываемую поверхность. Таким образом деталям придаются нужные формы и размеры.
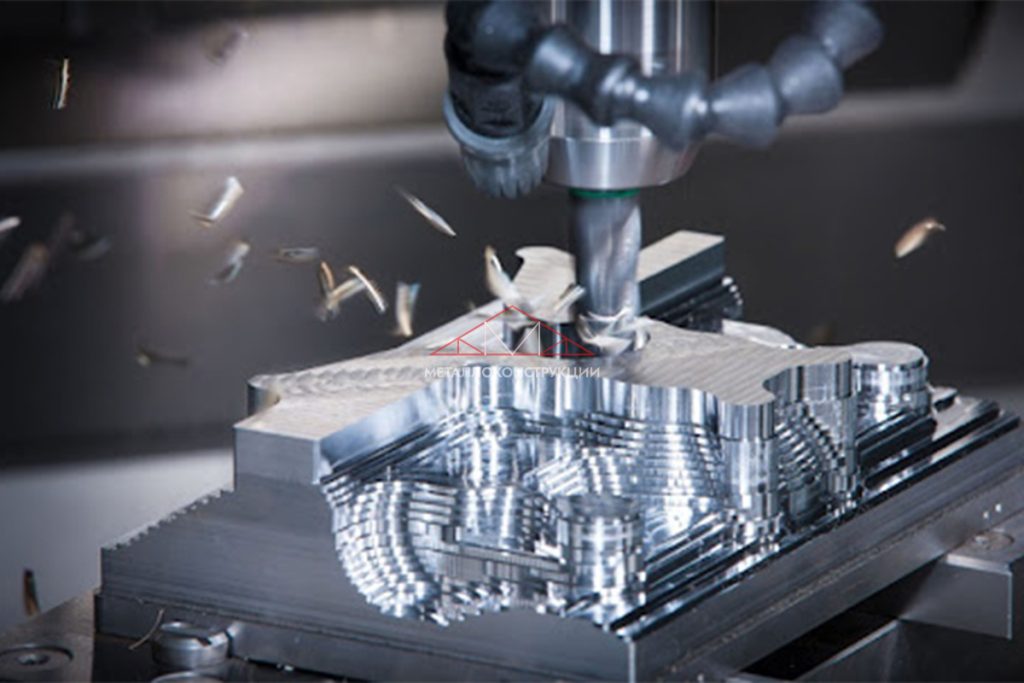
В современном производстве встречаются следующие типы механообработки:
- Точение. На токарном станке деталь жестко крепится и вращается вокруг своей оси, а резец снимает металл слой за слоем.
- Сверление. Заготовка жестко фиксируется в тисках и в ней сверлом проделывается отверстие. Размер зависит от параметров сверла.
- Фрезерование. Рабочая поверхность фрезы перемещается практически в любом направлении, благодаря чему детали придается желаемый вид.
- Строгание. Резец движется относительно поверхности, снимая продольную полоску. Применяется для создания продольных пазов.
- Шлифование. С помощью шлифовального круга, который крутится продольно, поперечно или вокруг заготовки ей придается определенный образ. В результате получается высокоточная деталь.
Преимущества:
- Точность — передовые станки оборудованы ЧПУ, что значительно повысило точность и тонкость работы, исключив из производства человеческий фактор;
- Постоянство — высокая автоматизированность процесса позволяет получать требуемые параметры раз за разом.
- Индивидуальность — современное производство открывает простор для реализации индивидуальных проектов и уникальных орнаментов.
Термическая обработка
Термообработка — это совокупность процессов по нагреву, выдержке и охлаждению металла и сплавов с различной скоростью в различных средах. В результате изменяется структура материала, заготовка получает запланированные физико-химические характеристики. Данный метод применяют для стали и цветных металлов.
Виды термообработки:
- Отжиг I-го и II-го рода. В зависимости от типа конкретного материала его нагревают до определенной температуры. Отжиг I-го типа отличается от II-го тем, что во втором случае происходят фазовые превращения, в результате чего повышается пластичность и вязкость, но ухудшается прочность и твердость металла.
- Закалка. Увеличивает прочность, износостойкость и твердость металла благодаря образованию неравновесной структуры. Применяется для материалов, которые при нагреве до высоких температур и последующем охлаждении проходят через фазовые превращения.
- Химико-термическая обработка. Происходит в среде, наполненной различными химикатами, изменяющими состав, структуру и характеристики изделия. В результате оно становится более износостойким и твердым, а также приобретает антикоррозийные свойства.
Преимущества:
- Универсальность — подходит для большинства известных металлов и сплавов;
- Улучшает характеристики — делая любую заготовку более твердой и износостойкой, повышая таким образом срок эксплуатации;
- Производительность — высокая скорость реакций позволяет использовать технологию в промышленных масштабах.
Сварка
Сварка — техника создания неразрывного соединения металлов путем их нагрева. Для создания шва часто используют присадочный материал, формирующий прочное соединение после своего остывания.
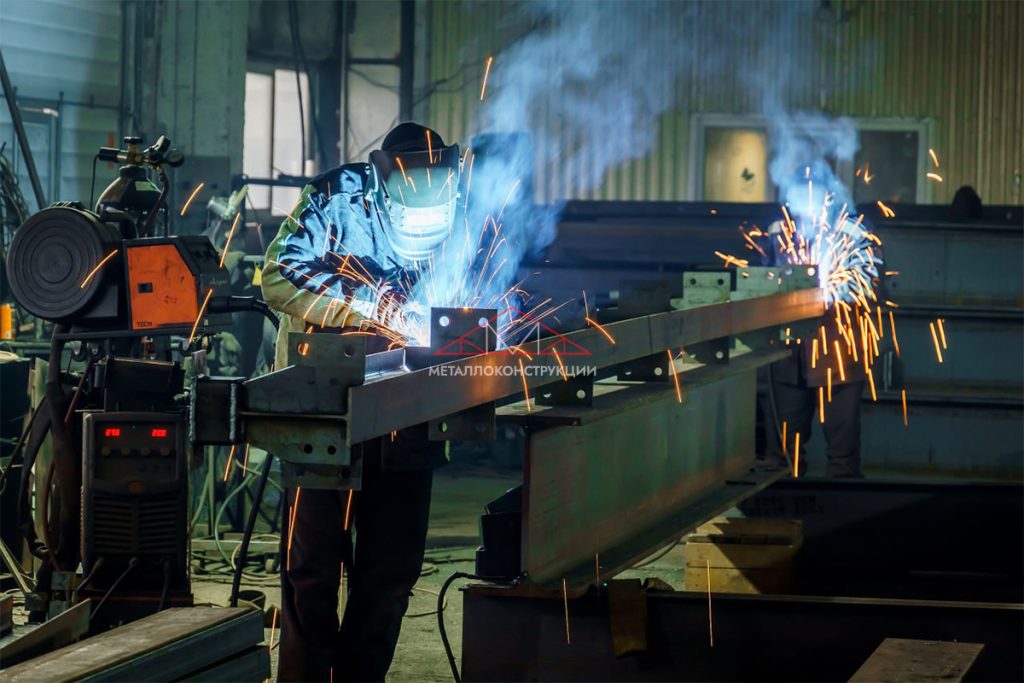
Для осуществления сварки требуется электрическая дуга, а также ультразвуковое и лазерное излучение. В зависимости от того, каким именно способом нагревают металл, выделяют следующие разновидности сварки:
- Химическая. Нагрев происходит от тепла химической реакции. Лучше всего подходит для сварки под водой или в труднодоступных местах.
- Газовая. Сварка происходит от пламени газовой горелки. Не самый безопасный способ обработки материала.
- Электрическая. Наиболее распространенная технология. Энергия электрической дуги нагревает и расплавляет рабочую зону. Существует точечная и роликовая электрическая сварка. В первом случае нагревание происходит в конкретной точке, во втором — шов образуется по месту движения ролика.
Преимущества:
- Прочность — швы по крепости часто превосходят остальные части конструкции;
- Диапазон работ — без сварочных технологий невозможна практически ни одна отрасль промышленности.
Электрическая обработка металла
Технология опирается на использование электричества для локального разрушения заготовки путем воздействия тока высокой интенсивности. Таким образом разрезают металлические листы толщиной до 35 мм.
В современном производстве популярностью пользуются оптоволоконные лазерные аппараты. Они отличаются высокой точностью и скоростью работы, минимальной зоной воздействия и способностью работать с тонкими материалами и сложными конструкциями. С помощью лазеров добиваются не только неразрывных соединений металлов, но и занимаются художественной резкой, создавая сложные орнаменты.
На нашем производстве мы используем 7 лазерных оптоволоконных станков и 2 плазменных станка для резки металла.
Преимущества:
- Точность — все оборудование оснащено ЧПУ, благодаря чему обеспечивается точность и аккуратность реза;
- Скорость — лазерные технологии не знают равных в скорости раскроя, поэтому они так актуальны для современного массового производства;
- Безопасность — на поверхность изделия не оказывается механического воздействия, что исключает риск брака заготовки.
Оставьте заявку прямо сейчас и получите подробное коммерческое предложение с расчётами и сроками производства металлоконструкций под ключ.
Оставить заявку